Waarschijnlijk ben jij in je werk actiegericht. Als je een probleem ziet, wil je het oplossen en het liefst zo snel mogelijk. Echter kan je jezelf de vraag stellen: los ik daadwerkelijk het probleem op of los ik de symptomen van het probleem op? Om daar achter te komen kan je een Root Cause Analyse uitvoeren.
Neem bijvoorbeeld een storing van een machine. Los je daadwerkelijk de storing op, of los je een symptoom op dat de storing veroorzaakt? Hoogstwaarschijnlijk draait je machine na het oplossen van een symptoom nog wel even door, maar een week later sta je weer voor hetzelfde probleem. Met RCA kom je erachter waar het probleem écht ligt en kan je het bij de kern aanpakken.
Waarom is RCA belangrijk voor de Technische Dienst?
De Technische Dienst krijgt regelmatig ingewikkelde problemen voor de kiezen, die niet zomaar op te lossen zijn door alleen naar de symptomen te kijken. Daarom is het belangrijk om naar de oorzaak van het probleem te kijken en een RCA uit te voeren. Door dit te doen, wordt je productie weer gestroomlijnd. Dit bespaart vervolgens behoorlijk wat tijd en geld, wat je anders kwijt zou zijn aan het uitstellen van een probleem.
Verschillende methodes
Er zijn verschillende methodes om RCA toe te passen. Hieronder lichten we drie methodes toe:
‘’Waarom-vraag’’
De ‘’waarom-vraag’’ stellen is een goede start om de oorzaak van een probleem te achterhalen. Deze vraag vormt dan ook min of meer de basis van RCA. Dit gebeurt alleen niet vaak, omdat je natuurlijk vertrouwt op de ervaring van de monteurs. Als er weer wat gesleuteld of gesmeerd is en de machine weer doet wat die moet doen, moet het opgelost zijn, toch?
Helaas kan het zo zijn dat je een week later weer met dezelfde storing zit. De grondoorzaak is dus nog niet opgelost. Probeer door 5 keer de waarom-vraag te stellen, te achterhalen waar die storing vandaan komt. In het begin lijkt het misschien wat flauw, maar uiteindelijk leidt het tot nuttige inzichten. Het kan er als volgt uitzien:
Waarom heeft machine X storing?
Omdat de motor van de machine plotseling is gestopt met draaien.
Waarom is de motor gestopt met draaien?
Omdat de temperatuur van de motor is gestegen tot een gevaarlijk niveau.
Waarom is de temperatuur van de motor gestegen?
Omdat de koelvloeistof niet correct circuleerde door het koelsysteem van de motor.
Waarom circuleerde de koelvloeistof niet correct?
Omdat de waterpomp van de motor defect is geraakt.
Waarom is de waterpomp defect geraakt?
Omdat een lager in de waterpomp is versleten door langdurig gebruik zonder onderhoud.
Nu had je allerlei pleisters kunnen plakken door de machine tijdelijk niet te gebruiken om de temperatuur van de motor omlaag te brengen. Of door de koelvloeistof te vervangen in de hoop dat het daardoor wel goed zou circuleren. Uiteindelijk had dit allemaal niet uitgemaakt, want de lager in de waterpomp zou het alsnog begeven hebben door slijtage.
Door deze methode kan je direct concluderen dat de lager in de waterpomp vervangen moet worden, om niet continu een storing te krijgen op machine X. Daarnaast kan je in de toekomst zuiniger zijn op de waterpomp, door bijvoorbeeld een smeerronde in te plannen. Met een onderhoudsbeheersysteem zou je dit preventieve onderhoud gemakkelijk kunnen invoeren. Hierdoor voorkom je overmatige wrijving en verleng je de levensduur van de waterpomp.
Ishikawa (visgraat) diagram
Een volgende methodiek voor RCA is het Ishikawa (visgraat) diagram. Het wordt niet voor niets een visgraatdiagram genoemd; het ziet eruit als een schematische weergave van het skelet van een vis. Hierdoor zie je in één oogopslag wat de mogelijke oorzaken van een probleem zijn. Deze methode dwingt je om vanuit verschillende perspectieven naar een probleem te kijken. Door vanuit deze verschillende perspectieven te kijken, voorkom je tunnelvisie. De categorieën zijn als volgt:
Mensen
Iedereen die betrokken is bij het proces
Methoden
Hoe het proces wordt uitgevoerd en de specifieke eisen die daarbij worden gesteld (beleid, regels, voorschriften en wetten)
Machines
Alle apparatuur, computers, gereedschappen etc. die nodig zijn om de taak te verrichten.
Materialen
Onderdelen, pennen, papier, enz. die gebruikt worden om het eindproduct te produceren.
Metingen
Gegevens gegenereerd uit het proces die worden gebruikt om de kwaliteit te evalueren.
Milieu (omgeving)
De voorwaarden, zoals locatie, tijd, temperatuur en de cultuur, de manier van werken, rondom het proces.
Samen met de Technische Dienst kan je per categorie brainstormen over de oorzaken. Sommige oorzaken kunnen worden ondergebracht in meerdere categorieën. In de laatste stap worden oplossingen gekozen en bepaald welke daarvan als eerste wordt doorgevoerd. Een ingevuld diagram zou er als volgt uit kunnen zien:
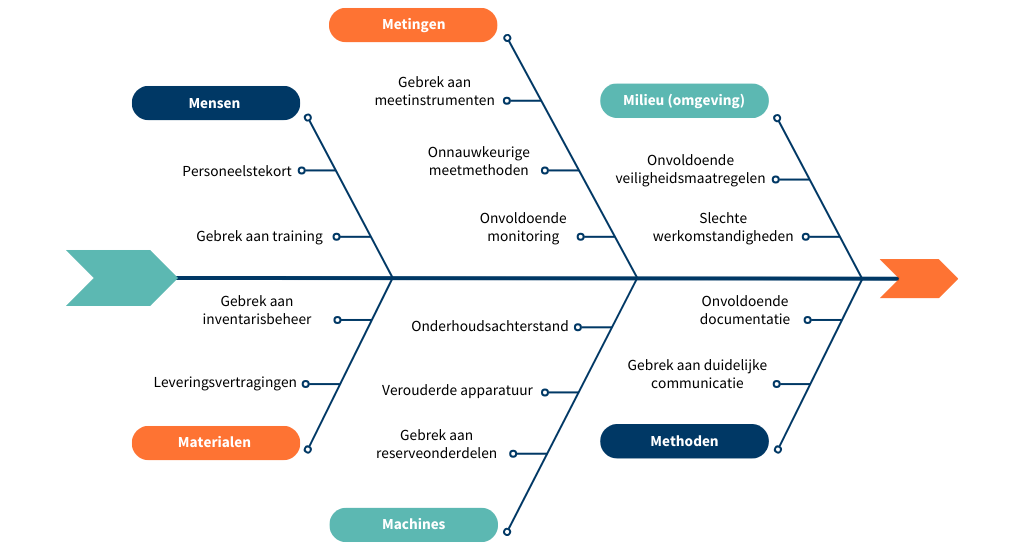
De probleemboom
Ook met een ‘probleemboom’ kun je een overzicht creëren van waar de grondoorzaken van een probleem liggen. Hieronder een voorbeeld.
Door het probleem steeds verder af te pellen, worden oorzaken en gevolgen in verband gebracht met elkaar. Een ‘probleemboom’ maakt vaak ook duidelijk dat er meerdere grondoorzaken zijn die een probleem veroorzaken.
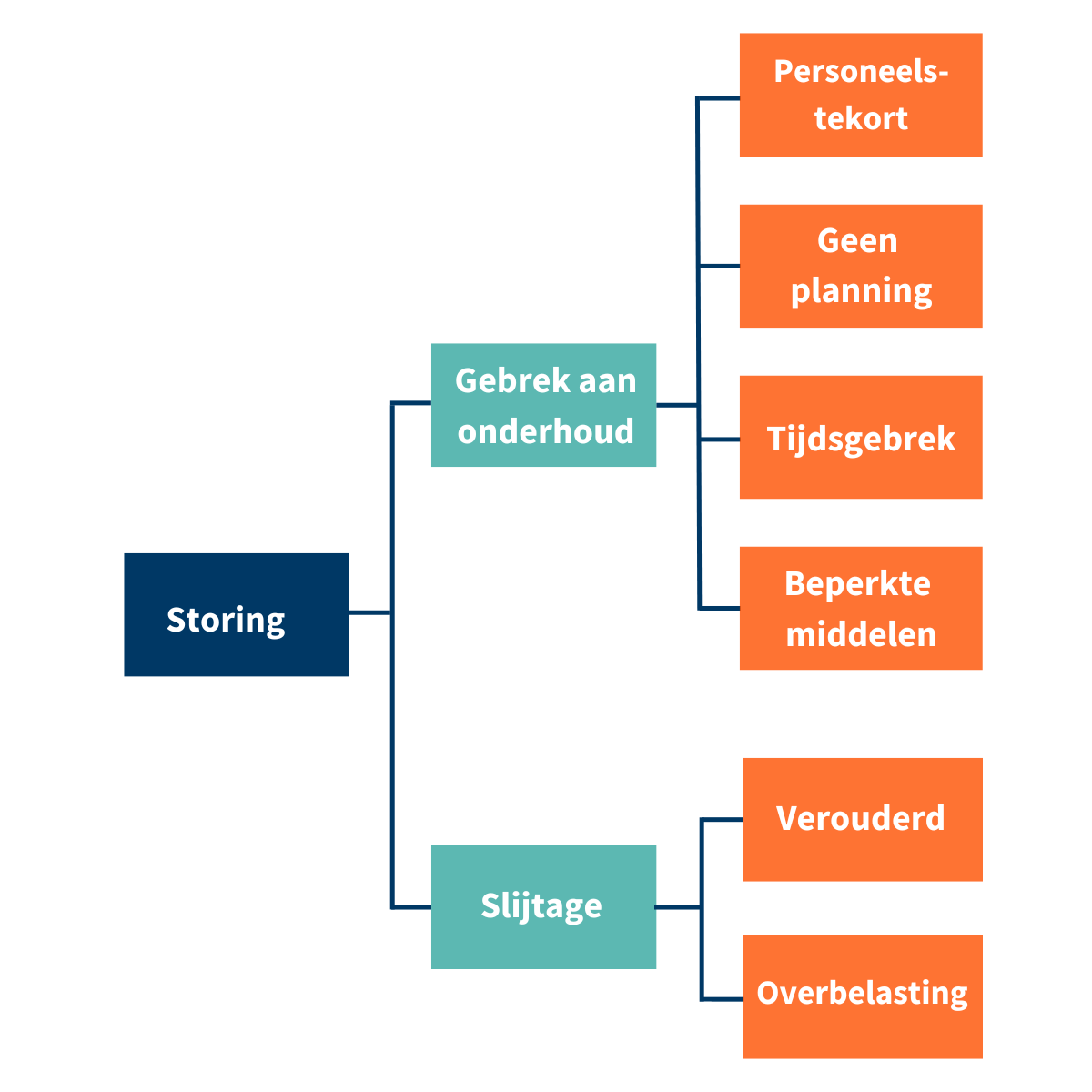
Start jij ook met RCA?
Root Cause Analyse (RCA) is een belangrijke stap voordat je aan de slag gaat met verbeteringen. Het hoeft niet moeilijk te zijn of lang te duren, zolang je er maar bewust mee bezig bent. Toch is de verleiding soms groot om snel aan de slag te gaan en RCA over te slaan. Dat is begrijpelijk, maar het kan verspilde tijd en energie voorkomen. Het helpt je te voorkomen dat je verbeteringen probeert te maken die uiteindelijk niet veel helpen.
RCA toepassen en preventief onderhoud uitvoeren met McMain
Het toepassen van RCA in combinatie met preventief onderhoud kan leiden tot aanzienlijke verbeteringen in de betrouwbaarheid van je apparatuur. Met het onderhoudsbeheersysteem van McMain heb je de juiste tool in handen om RCA toe te passen en preventief onderhoud in te plannen. Zelf uitproberen? Dat kan met de gratis 30 dagen trial van McMain Online. Je krijgt dan toegang tot alle functionaliteiten van de software zodat je deze zelf kunt uitproberen. Heb je hier vragen over of wil je meer weten over digitaal onderhoudsbeheer? Neem dan contact met ons op via +31(0)341-750 500 of [email protected]. We staan voor je klaar!