Stel je voor: je staat in de werkplaats en moet snel een specifieke sleutel of een meetinstrument vinden, maar de werkbank ligt vol met gereedschap en oude onderdelen. Of je wilt onderhoud uitvoeren aan een machine, maar de benodigde onderdelen liggen verspreid in het magazijn. Dit zorgt niet alleen voor frustratie, maar kost ook onnodig veel tijd en kan zelfs fouten veroorzaken.
Dit is precies waarom de 5S-methode is ontwikkeld. Oorspronkelijk afkomstig uit de maakindustrie, helpt deze methode jou om je werkplek efficiënt, overzichtelijk en veilig te houden. Hierdoor heb je minder verspilling en verhoogde productiviteit.
Hoe de 5S-methode ontstond uit het Toyota Production System
Deze methode werd voor het eerst toegepast in de Japanse auto-industrie. Oorspronkelijk maakte het deel uit van het Toyota Production System (TPS), ontwikkeld door Toyota in de jaren 50 om flexibeler te werken in een concurrerende markt. Toyota wilde elk onderdeel van het autoproductieproces weghalen dat bijdroeg aan ‘muda’, het Japanse woord voor ‘afval’.
Een belangrijk onderdeel van deze strategie was het herinrichten en organiseren van de werkvloer. Met name om het consistent en ordelijk te houden. Dit minimaliseerde de hoeveelheid tijd die besteed werd aan het zoeken naar gereedschap en apparatuur. Het verminderde ook onnodige verplaatsingen die de focus weghaalden van de kerntaken.
De 5 stappen naar een georganiseerde werkplaats
Naarmate het TPS-framework zich ontwikkelde, ontstonden vijf kernfocusgebieden, elk met een Japanse naam beginnend met een “S”. Dit vormde de basis voor de naam 5S. Deze termen beschrijven de opeenvolgende stappen van het 5S-systeem:
1. Seiri: uitzoeken en elimineren wat niet echt nodig is
2. Seiton: ordenen wat overblijft na sortering
3. Seisou: het werkgebied schoonmaken en inspecteren
4. Seiketsu: standaarden creëren die een herhaalbaar proces ondersteunen
5. Shitsuke: deze normen consequent toepassen op alle werkgebieden
Het Toyota Production System verhoogde de productiviteit aanzienlijk. Al snel namen westerse productiebedrijven het over en groeide 5S uit tot een breed toegepast principe. De originele Japanse termen zijn vertaald naar Nederlandse termen, die ook met een “S” beginnen:
1. Scheiden
2. Schikken
3. Schoonmaken
4. Standaardiseren
5. Standhouden
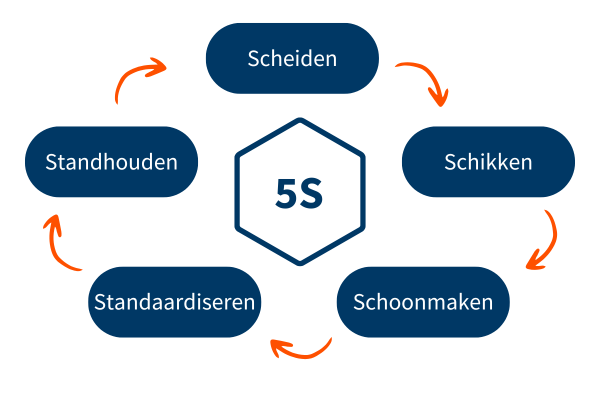
Zo pas je de 5S-methode toe
Maar waar begin je? Wat is de eerste stap om deze methode succesvol te implementeren? En hoe zorg je ervoor dat je team niet alleen meedoet, maar ook enthousiast blijft over deze werkwijze?
1. Scheiden
Tijdens deze stap bepaal je welke items in je werkruimte echt nodig zijn en welke niet of mogelijk overbodig zijn. De essentiële items houd je binnen handbereik, terwijl je de overige items verplaatst naar een ander opslaggebied.
Waarom scheiden?
Scheiden creëert een productievere werkruimte door onnodige rommel te verwijderen (en afleidingen weg te halen). Het is ook een eerste stap naar het vrijmaken van ruimte voor andere doeleinden. Plan een moment in en moedig je team aan om alles in hun werkruimte kritisch te bekijken. Laat ze bepalen of elk item echt nodig is voor hun dagelijkse werk.
2. Schikken
In deze stap organiseer je de overgebleven spullen op een logische manier. Veelgebruikte items blijven binnen handbereik, terwijl elk item een vaste, goed vindbare plek krijgt.
Waarom schikken?
Schikken betekent dat alles een vaste, logische plek krijgt, zodat je het snel kan vinden en makkelijk terug kan leggen. Dit voorkomt onnodig zoeken en zorgt ervoor dat spullen op een handige, ergonomische plek staan. Bovendien helpt het om ruimte vrij te maken die je slimmer kan gebruiken om de workflow te verbeteren.
3. Schoonmaken
Deze stap maakt je werkplek niet alleen schoner, maar ook beter georganiseerd. Maak gereedschap, apparatuur en andere spullen grondig schoon en controleer het goed. Dit kan ook klein onderhoud aan machines betekenen, wat mooi aansluit op TPM.
Waarom schoonmaken?
Door schoon te maken creëer je een werkomgeving die aanspreekt en het fijner maakt om in te werken. Het helpt ook om problemen te identificeren voordat ze de productie verstoren. In een schone werkomgeving is het bijvoorbeeld veel gemakkelijker om opkomende problemen te signaleren, zoals vloeistof lekken, gemorste materialen, metaalsplinters door onverwachte slijtage, enzovoort.
4. Standaardiseren
Met deze stap verbind je de eerste drie 5S-stappen (Scheiden, Schikken, Schoonmaken) met de laatste stap (Standhouden). Het doel is om de beste 5S-werkwijzen vast te leggen en ervoor te zorgen dat je team ze als vaste standaard hanteert.
Waarom standaardiseren?
Standaardiseren zorgt ervoor dat 5S een blijvend proces wordt. Het verandert 5S van een eenmalige opruimactie in een routine die steeds herhaald kan worden.
5. Standhouden
Deze stap zorgt ervoor dat 5S een blijvend onderdeel van de werkcultuur wordt. Het maakt van de gestandaardiseerde 5S-processen vaste, terugkerende gewoontes.
Waarom standhouden?
Zodra de standaarden zijn vastgesteld, is het belangrijk om ze consequent toe te passen. Het volhouden van de 5S-methode draait om het behouden van het proces en tegelijkertijd blijven verbeteren. Zo kan je langer genieten van je veilige, schone omgeving.
McMain en de 5S-methode versterken elkaar
Door 5S te combineren met de CMMS-software van McMain kan je niet alleen je werkplek efficiënter en veiliger maken, maar ook structureel onderhoud en verbetering waarborgen. Met inspectielijsten voer je periodieke controles uit om orde en netheid te behouden. Preventief onderhoud helpt bij het plannen van reiniging en onderhoud, zodat de werkomgeving gestructureerd blijft. Documentbeheer zorgt ervoor dat 5S-checklists en schoonmaakschema’s digitaal worden bijgehouden voor standaardisatie. Dankzij mobiele toegang kunnen inspecties ter plaatse worden uitgevoerd en verbeterpunten direct worden geregistreerd.
Zelf uitproberen?
Vraag een gratis 30 dagen trial aan van McMain Online. Je krijgt dan toegang tot alle functionaliteiten van de software zodat je deze zelf kunt uitproberen. Heb je hier vragen over of wil je meer weten over digitaal onderhoudsbeheer? Neem dan contact met ons op via +31(0)341-750 500 of [email protected]. We staan voor je klaar!